Casting is one of the oldest production methods used to manufacture products that are generally difficult or costly to produce by other methods. It is divided into classes such as sand mold casting, permanent mold casting, plaster mold casting, precision casting, continuous casting and centrifugal casting. Among these, the more traditional sand mold casting method is the most preferred in terms of both economy and ergonomics.
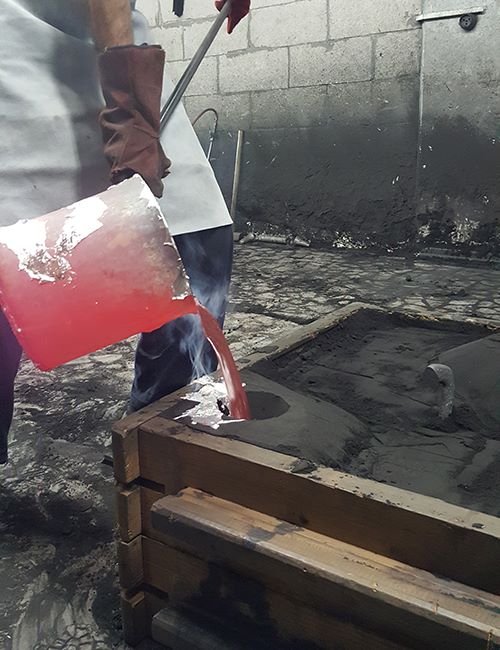
Sand Mold Casting Methods
Sand mold casting method is also divided into different categories. Now let's look at each method and its advantages and disadvantages.
Green Sand Mold Casting
It is a sand mold casting method widely used in foundries. The liquefied metal is poured into a reusable mold and kept in the mold until the solidification process is complete. At the end of this process, the mold is opened and the product is removed.
Advantages of Green Sand Mold Casting Method
- The mold material used in this method is cleaned and made reusable for other applications. This shows that it is one of the most economical casting methods.
- It has a simple mechanism. Development can be done on the system easily.
- It is possible to transform different types of metals into a design-product by casting.
Disadvantages and Limitations of Green Sand Mold Casting Method
- During the casting of large parts with complex shapes and parts with long and thin designs, the mold strength may not give the expected results.
- Since the mold must be moved during the process, mold failure is possible.
- Dimensional tolerances are lower than other basic sand mold casting methods.
Dry Sand Mold Casting
Soot sand molds, which are produced in a similar way to the production of green sand molds, are subjected to a drying process at temperatures not exceeding 350 ˚C. In order to preserve the moisture of the clay that provides the binding force of the mold material, it should not be exposed to high temperatures. Otherwise, it may negatively affect the strength of the mold material.
Advantages of Dry Sand Mold Casting Method
- Its resistance to metal erosion is superior to other sand mold casting methods.
- The probability of the mold being damaged during transportation is lower.
- When less permeable mold material is used, the surface quality is better.
- Humidity control is not very important in the molding process.
- Casting defects are less. This is because there is no steam formation during casting.
Disadvantages of the Sand Mold Casting Method
- Since the surface drying process in this method extends the process, there is an increase in production costs.
Dried Molds
Casting defects can be reduced by surface treatments applied to green sand molds. A blower, an electric heater or a different type of machine that provides hot air can be used in this process. A layer of 6 to 25 mm is usually dried on the mold surface, which minimizes mold problems that may arise due to moisture.
Advantages of Dried Molds
- Casting errors are less.
- Desired surface quality is obtained.
Disadvantages of Dried Molds
- When drying is done with a heat source, there may be an increase in humidity in direct proportion to the increase in temperature.
Hollow Molds
Hollow molds are used for the production of parts that are too large to fit into the mold degrees. Generally, products ranging from 1 to 100 tons can be obtained. Large mold cavities, namely the pits in this method, are needed for the production of large parts. These pits, which resemble pools, can reach several meters in depth, width and height depending on the size of the part.
Advantages of Hollow Molds
- It is possible to produce products of sizes that cannot be produced with other sand mold casting methods.
- High quality can be achieved in products produced by expert mold makers.
Disadvantages of Hollow Molds
- Making a mold can take days or even weeks.
- Cost is high for parts produced in limited quantities.
- As both an advantage and a limitation, product quality in this method depends largely on the molders involved in the project.
Molds Prepared with CO₂ Method
We can classify this method somewhere between wet and sand molding. It is a relatively more modern method. In many sources, it is referred to as the CO₂ - Sodium Silicate Method or CO₂ hardening.
The method is based on the hardening of cores and molds with CO₂. Carbon dioxide gas converts sodium silicate into silica gel, which allows the sand grains to reach the desired bonding level. In other words, molds are hardened or hardened sections are combined to ensure mold integrity. The casting process must be carried out within 24 hours after the mold is ready.
Advantages of Molds Prepared with CO₂ Method
- High strength values can be achieved.
- It is a method suitable for almost all casting alloys.
- It does not require expensive equipment.
- The surface quality and dimensional tolerances of the part coming out of the mold – dimensional accuracy is superior to other sand molding methods.
Disadvantages of Molds Prepared with the CO₂ Method
- The molds take 24 hours to break down. The casting process must be carried out within this time, and this requires good teamwork.
- There is a possibility that the cores and mold may disintegrate following the casting process.